So for the first two months of my DIY Catalyst stay at The Edge, I have been devouring everything related to 3D printing. Anyone curious enough to stop and chat has been bombarded by me waxing lyrically about how consumer 3D printing is going to radically change the manufacturing landscape. Consumer 3D fabrication will lower labour costs to a point where mass customisation will become a viable replacement for almost everything that is mass produced today.
The 3D fabrication revolution will mean that you will no longer need to battle the weekend crowds and dodgy meatballs of your local Scandinavian furniture store. Instead of traveling to a warehouse to purchase mass produced flat-pack furniture, you will browse an online catalog of furniture templates and select a design that is the closest match to what you are after. You will purchase and download the design in exactly the same way you currently purchase from online app, music and game stores. However, once the download is completed, then the real fun would begin. You would have the freedom to completely customise every aspect of the furniture’s design. Is the default too wide to fit in your room? No problems, just squeeze the digital design and make it fit! Did you actually want the legs to be the same as your grandmothers antique dressing table? No dramas, just take a picture, trace out a copy and replace the legs. All happy with your design? Now just hit print and assemble as you would with any other flat-pack furniture design.
So mid rant, a friend of mine suddenly went from a blank look to the wild eyes of a mad scientist that had just concieved the perfect way to end that pesky Mr Bond once and for all. He bursts in “I get it! That is totally cool, in fact I broke my fine scandinavian lamp just the other week. Do you think you could print a replacement part?”
I wasn’t sure, but was keen to have a try all the same. I sat down with a pair of digital calipers, measuring up all the different dimensions of the busted component. These measurements were converted into a digital design I created using the open source computer aided design tool FreeCAD. From here it went for a short hop through RepSnapper and was printed on a Mendel RepRap. The printed replacement worked perfectly, and my friend did not have to throw away a whole lamp because a small plastic component snapped.

When we realised that the lamp part was going to work, it got me thinking: Pixar managed to go from the 2 minute 3D “short” Luxo Jr to the 81 minute, full length feature film Toy Story… In just nine freaking years. A remarkable achievement, one that required a huge amount of technology to be invented, assembled and cordinated that revolutionised the animation industry. I think the same will apply for consumer 3D fabrication. In just a decade, we will witness a revolution in manufacturing and evolve past simple printed replacement parts, to a world where furniture is downloaded, remixed and customised on a scale that has never been achieved before. Art Nouveau for the new millenium? Hell yes!
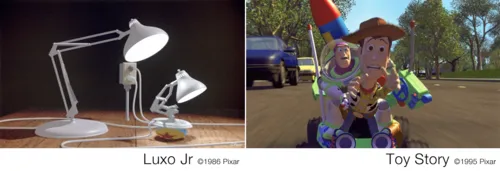
Originally posted on The Edge blog.
Comments:
You can join the conversation on Twitter or Instagram
Become a Patreon to get early and behind-the-scenes access along with email notifications for each new post.
Hi! Subconsciously you already know this, but let's make it obvious. Hopefully this article was helpful. You might also find yourself following a link to Amazon to learn more about parts or equipment. If you end up placing an order, I make a couple of dollarydoos. We aren't talking a rapper lifestyle of supercars and yachts, but it does help pay for the stuff you see here. So to everyone that supports this place - thank you.