Hello.
Clinton Freeman is a new media artist working out of Queensland, Australia. He draws upon experience as a classically trained software engineer to create interactive works that explore the blurry frontiers of science. By imbuing software and electronics with the warmth of our analog past, Clinton makes technology that’s less machine and more human.
With an extensive back catalog filled with collaborations and commissions, his digital systems have powered many award-winning immersive works.
Latest
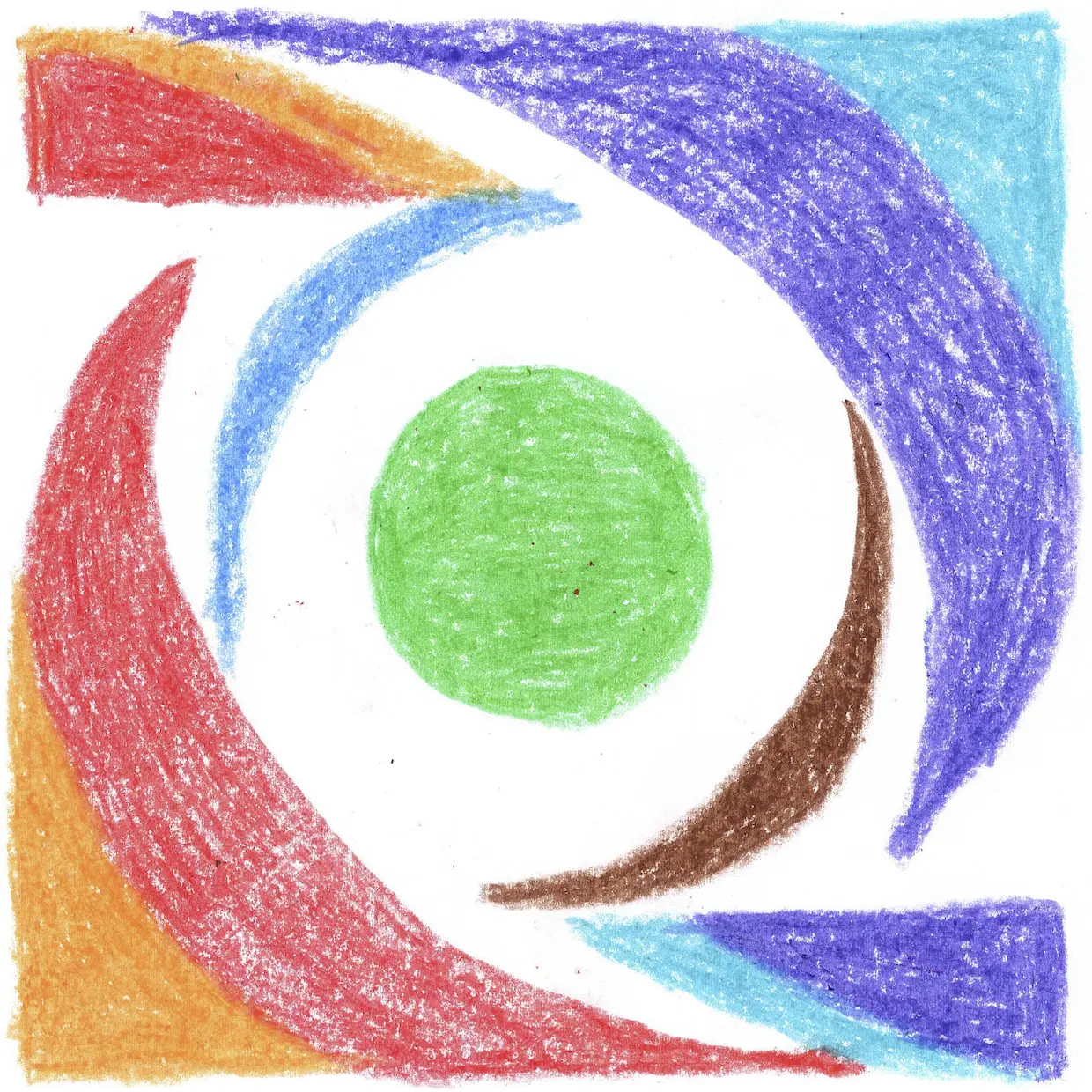
The Imperfect Perfection of AI - Uncovering the Human Side of Algorithms
Exploring the subtle imperfections of AI-generated content, this essay examines how algorithms conceal their flaws and why our humanity surfaces precisely in our imperfections—highlighted by Kasparov's historic chess match with Deep Blue.
Articles
I find writing helpful and share my articles so they can be useful to others. You will find a complete list in the directory.
Hi! Subconsciously you already know this, but let's make it obvious. Hopefully this article was helpful. You might also find yourself following a link to Amazon to learn more about parts or equipment. If you end up placing an order, I make a couple of dollarydoos. We aren't talking a rapper lifestyle of supercars and yachts, but it does help pay for the stuff you see here. So to everyone that supports this place - thank you.